What is the bullwhip effect?
The bullwhip effect is a supply chain phenomenon describing how small fluctuations in demand at the retail level can cause progressively larger fluctuations in demand at the wholesale, distributor, manufacturer and raw material supplier levels. The effect is named after the physics involved in cracking a whip. When the person holding the whip snaps their wrist, the relatively small movement causes the whip's wave patterns to increasingly amplify in a chain reaction.
In supply chain management, customers, suppliers, manufacturers and salespeople all have only a partial understanding of actual demand and direct control over only part of the supply chain. However, each influences the entire chain with their forecasting inaccuracies by ordering too much or too little. A change in any link along the supply chain can have a profound ripple effect on the rest of the supply chain. Given that, there are many contributors and causes of the bullwhip effect in supply chain management.
Due to a lack of communication between the different parties involved in a supply chain, a bullwhip effect can cause serious challenges, such as excessive investment in inventory, lost revenue, declines in customer service, delayed schedules and even layoffs or bankruptcies.
How to identify the bullwhip effect
The bullwhip effect is observed in a wide range of supply chain-operating businesses, particularly in areas where demand is known to fluctuate, such as consumer electronics, fashion and medicine.
However, it isn't easy to identify, especially in real time, since it's caused by a lack of communication between the various parties involved in the supply chain. Also, this phenomenon is often observed after its negative effects have already trickled down the supply chain and have caused inefficiencies.
Organizations and manufacturers can potentially identify the bullwhip effect by analyzing order patterns, inventory data and lead time variability across different supply chain stages to determine where and how demand variability is amplified in the supply chain.
A simplified example of the bullwhip effect
The bullwhip effect often occurs when retailers become highly reactive to demand, and in turn, amplify expectations around it, which causes a domino effect along the supply chain. Suppose, for example, a retailer typically keeps 100 six-packs of one soda brand in stock. If it normally sells 20 six-packs a day, it will order that replacement amount from the distributor. But one day, the retailer sells 70 six-packs and assumes customers will start buying more products. They respond by ordering 100 six-packs to meet this higher forecasted demand.
The distributor might then respond by ordering double, or 200 six-packs, from the manufacturer to ensure they don't run out. The manufacturer then produces 250 six-packs to be on the safe side. In the end, the increased demand has amplified the supply chain from 100 six-packs at the customer level to 250 six-packs at the manufacturer.
This example is highly simplified but conveys the sense of exponentially increasing misalignment as actions and reactions continue up and down the chain. The bullwhip effect also occurs because of lowered demand at the customer level, which causes shortages when inaccurate and can be caused at other places along the chain.
A classic real-world example of the bullwhip effect happened with toilet paper shortages during the COVID-19 pandemic. Stores rapidly escalated order quantities to meet panicked consumer demand, prompting manufacturers upstream to ramp up production. This spike in demand was driven by short-term consumer stockpiling in response to the pandemic.
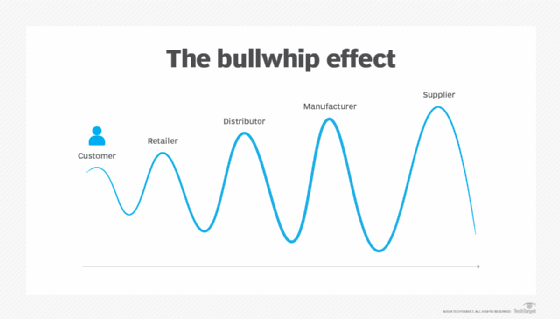
Causes of the bullwhip effect
Companies must forecast customer demand based on insufficient demand information and try to predict how much product customers will actually want while accounting for the complex factors that enable that amount to be delivered correctly and on time. At every stage of the supply chain, there are possible fluctuations and disruptions, which influence the myriad supplier orders.
Changes in customer demand directly influence all the other factors along the chain, including inventory. However, the bullwhip effect can occur even in relatively stable markets where the demand is essentially constant.
Forecasting demand has always been a difficult endeavor. The increasing complexity of today's global supply chains intensifies that difficulty, as does increasing consumer preference for omnichannel and e-commerce. A few of the most common dependencies that can cause a bullwhip effect include the following:
- Lead-time issues, such as manufacturing delays.
- Less-than-optimal decisions made by supply chain stakeholders at any point along the chain; for example, customer service or shipping.
- A lack of communication and alignment between each link or stakeholder organization in the supply chain.
- Over- or under-reacting to demand expectations, such as ordering too many units or not enough.
- Customer companies -- often retailers -- combine orders and let them build up before placing orders with their suppliers, a practice called order batching.
- Unexpected spikes in customer demand, poor inventory management and other issues that start small at the supplier level and spread across the entire supply chain.
- Discounts, cost changes and other price variations that disrupt regular buying patterns.
- Inaccurate forecasts from over-reliance on historical demand to predict future demand.
The bullwhip effect's implications on supply chain management
The bullwhip effect has historically caused disruptions and can be costly to all the organizations in the supply chain. Excess inventory can result in waste, while insufficient inventory can lead to reduced lead time, poor customer experience and lost business.
Most businesses use safety stock or reserve inventory as a buffer against demand fluctuations. However, safety stock isn't a remedy for the bullwhip effect. However, it provides enough product to fill orders until more arrives from suppliers.
The key challenges caused by the bullwhip effect on the supply chain include the following:
- Excessive inventory. Excessive inventory is a common side effect of the bullwhip effect. Depending on the product type, excessive inventory can produce significant waste or change in the cost of products. For example, perishable items, such as food and pharmaceuticals, can expire before they're sold. Similarly, certain items such as technological products can get replaced by newer versions or products before being sold. The diminished value of the items can necessitate the need for clearance or the loss of items that need to be discarded.
- Increased storage costs. The bullwhip effect can cause a spike in production levels, which automatically increases the amount of inventory that needs to be stored. Overstocked items and excessive inventory that can't be sold within a certain timeframe can incur high storage costs. Inventory can also lose its value if it isn't sold before its demand declines.
- Customer dissatisfaction. The bullwhip effect can cause businesses to struggle with inaccurate demand forecasting, affecting their ability to meet customer demand consistently. This leads to missed sales opportunities and lower customer satisfaction, along with increasing costs associated with stockouts and backorders over time.
- Increased labor costs. Overstocking often leads to higher labor costs for managing an overloaded warehouse, involving costs for handling, sorting and selling surplus inventory. On the other hand, stockouts can also result in higher labor demands, as workers would need to work harder to come up with substitutes and product alternatives.
How to reduce the bullwhip effect
Better information is necessary to reduce the bullwhip effect. This means better communication among supply chain partners and better forecasting methods.
Some commonly recommended actions for reducing the bullwhip effect include the following:
- Foster supply chain communication and collaboration. Better alignment around supply chain issues is needed both within companies and among customers, suppliers, distributors, manufacturing and other partners. When suppliers understand customer needs, they can reduce excessive inventory. Supplier and project portals, Electronic Data Interchange transactions and other capabilities of supply chain management software can help.
- Use forecasting and visibility tools. A wide range of software enables more accurate demand forecasts and visibility into what's happening along the supply chain. This includes demand-sensing software, forecasting software, inventory optimization software, tools that use analytics -- especially predictive analytics, artificial intelligence and internet of things connectivity.
- Explore a demand-driven approach to supply chain management. A demand-driven approach relies on a system of coordinated technologies and processes to gain insight into supply chain occurrences and react to them quickly. It uses many of the approaches mentioned previously, especially collaboration and communication as well as new technologies to enable supply chain visibility, for a coordinated holistic approach. Each company must decide on the right push-pull approach to its strategy, where a push approach is used for stable products and a pull approach is used for those with more erratic demand.
- Enhance transparency among suppliers, customers and partners. Transparency is crucial in mitigating the bullwhip effect by improving the accuracy of information flow across supply chain providers. It provides clear visibility into demand and inventory levels, thereby helping to prevent overproduction, excess inventory and stock-outs. All stakeholders should be aware of the needs of the end customers and companies in each tier. They should also be aware of the outstanding inventory of their suppliers and customers.
- Explore improved approaches by adopting advanced forecasting methods. Companies should use advanced forecasting methods to streamline operations and reduce the bullwhip effect. For example, executing a vendor-managed inventory strategy enables vendors to make inventory decisions based on comprehensive, unbiased perspectives, unlike retailers that typically assess demand on a local level.
- Limit price fluctuations. Companies should minimize price fluctuations by reviewing their promotional strategy. Since frequent promotions can disrupt customer purchasing behavior, their frequency should be limited to enhance demand predictability. Companies should also strategically plan promotions and integrate them more effectively into their forecasting processes for optimal results.
Lessons on the bullwhip effect using the beer game
Originally developed at the Massachusetts Institute of Technology Sloan School of Management in the 1960s as an in-person game, the beer distribution game is a role-play simulation game -- no beer is involved -- in which players experience firsthand the complexity of supply chain management. It simulates the beer supply chain using retailer, wholesaler, distributor and brewer. The goal is to keep operating costs as low as possible, and teams are penalized for having too much inventory.
Fully remote, in-person or hybrid players can only communicate by relaying orders through the normal channels, mimicking a real-life supply chain and they must deal with inventories and backlogs as well as their effect on the bottom line. Among its lessons, the game illustrates the complexity of the system as a whole and the difficulty of making correct choices with limited information as well as quickly bringing to life the bullwhip effect in action.
Explore the supply chain risks companies face today and effective strategies to mitigate them. Gain insights into managing complex supplier relationships and navigating disruptions to ensure enhanced resilience and continuity.